BJ Minson’s path to success included a fork in the road. Fortunate for many, the founder and CEO of GRIP6 Belt Company chose to simultaneously take both the right and the left roads. The road on the right would carry him toward cutting-edge mircrofluidics. The road on the left was to satisfy an itch, the kind you get when you feel something just isn’t right
(Pictured: After obsessing about Tesla for the past six years, Minson finally took delivery of his Model 3 last July. He was just a tad bit excited.)
As a master’s student, Minson was creating microfluidic chip designs and waiting for E. coli colonies to grow. But between rounds, his mind was on product design. He had an idea to use the CO2 laser in his lab to test out thin plastic belt buckle concepts. “I simply wanted a better belt, one that didn’t have holes, didn’t have a flap hanging off and wouldn’t stick out under my shirt,” he said.
Within a few weeks, the prototypes were taking shape and working well. Next, he began cutting out aluminum parts on the water-jet cutter in the advanced machine shop and giving them to friends to try out. The new buckle design worked well, and the feedback was encouraging.
After graduating with his master’s and still on his chosen career path, Minson began a job working as an engineer at Merit Sensor Systems. By day, he was designing new manufacturing techniques for high volume blood pressure sensors, and by night he was refining the design and manufacturing techniques for his new belt.
His best friend gave him $1,000 to purchase a few supplies so he could launch the belt on Kickstarter to test the viability of the product. With no marketing, the belt raised $106,000 in 30 days. When the number reached nearly 10,000 units, manufacturing them in his garage no longer seemed feasible.
“The advice I received at the time,” said Minson, “is that I would not succeed without making my products in China, but something bothered me about that. Why did so many people think it was impossible to make products domestically? Why should I have to rely on someone halfway around the world to be successful? After all, I had specifically designed the belt to be simple to both use and manufacture. After about the 10th time. someone said I would fail without China. I was determined to prove them wrong.“
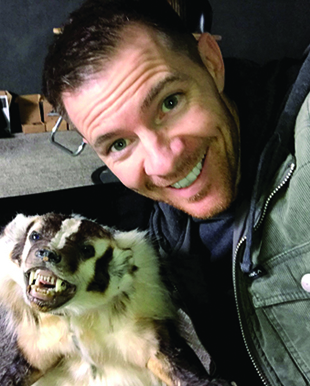
So GRIP6 was born in his garage. Minson buckled down and got friends and family to help him for free. Over the next several months, he purchased a few small machines, made several custom machines and pumped out belts and buckles. The labor and the long hours, in addition to a full day at work, made it a truly hellish experience, he said. However, the small team delivered on their promise and shipped GRIP6 belts all over the world.
BJ’s Tips For Engineering Students:
Be a project-oriented engineer. It’s critical to have a solid understanding of underlying principles, but you also have to move beyond the theory and get experience building physical things by hand. My most valuable engineers are the very diverse and adaptable type. They can’t help but work on their own projects on the side. They love learning and doing. School projects and personal projects and extremely valuable catalysts for learning and becoming valuable as an engineer.

Interesting things: Fun facts about BJ:
- BJ is obsessed with anything related to Elon Musk, Tesla and SpaceX.
- BJ coaches a small First Lego League team consisting of his daughters and nephews.
- BJ designs and builds electric scooters with and for his kids every summer.
- BJ cuts his own hair.
- BJ actively encourages engineering among youth; GRIP6 held its first annual “Engineering Day” for kids last summer, and plans to expand it in 2019 and beyond.